Printing 3D Objects with Interlocking Parts
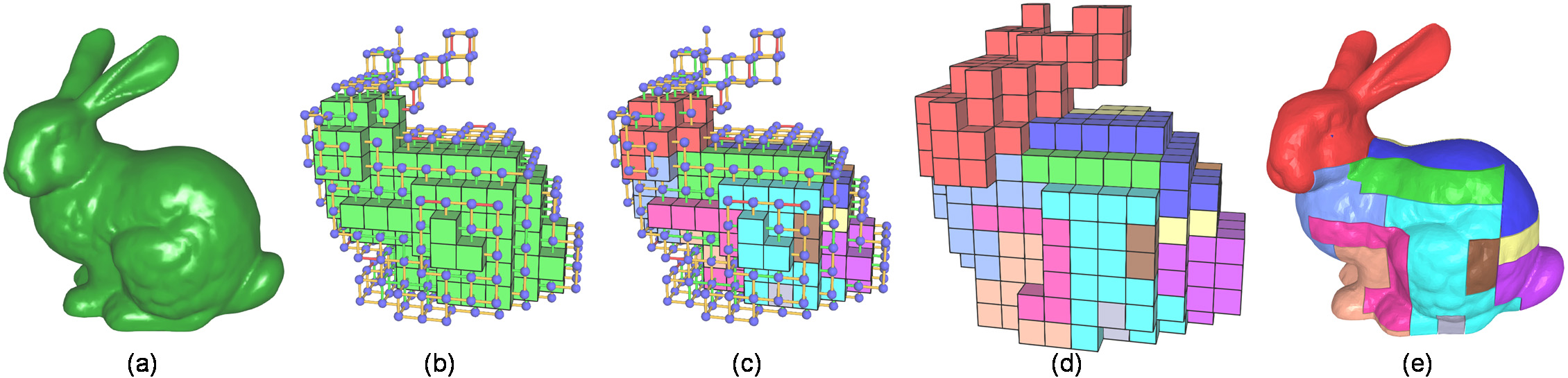
Figure 1: Overview. (a) A 3D watertight model as input; (b) voxelization and shape analysis; (c) creating initial interlocking parts; (d) attaching boundary voxels to the parts; and (e) refining the parts' geometry by CSG intersection with the input mesh model.
Abstract:
Recent advances in 3D printing technologies bring wide range of applications from fast prototyping to product manufacturing. However, one intrinsic limitation of 3D printing is that we cannot fabricate a single object that is larger than the working volume of a 3D printer. To address this issue, we may partition the given object into 3D parts of manageable sizes for printing, and then assemble the object from the printed 3D parts. Rather than using connectors, glue, or skew, we propose to connect the printed 3D parts by 3D interlocking such that the assembled object can be not only repeatedly disassembled and reassembled, but also strongly connected by the parts' own geometry. To achieve these, we develop a voxelization-based approach to partition a given 3D model into 3D interlocking parts. To guarantee the generated 3D parts to be structurally sound and well-connected by 3D interlocking, we deform the local geometry of the 3D model to avoid voxel fragmentation, employ internal voxels to create initial interlocking parts, and analyze the local shape within voxels to guide the final parts construction. We demonstrate the eectiveness of our approach on 3D models with a variety of shapes, and realize some of them by 3D printing.
Paper:
High Res (9Mb)–14 pages PDF download
Low Res (1Mb)–14 pages PDF download
Video:
Images:
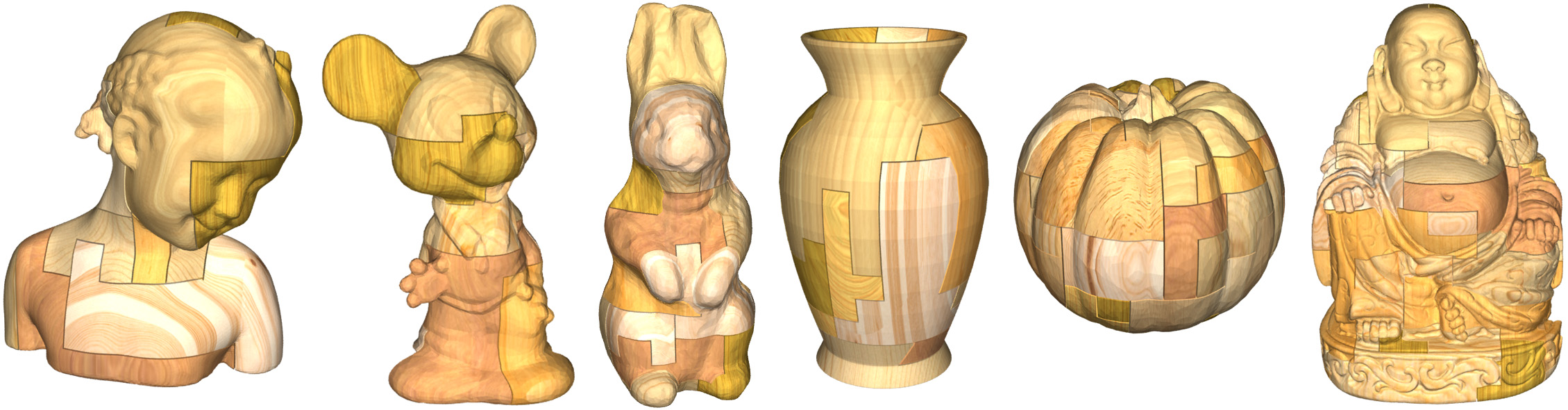
Figure 2: Various 3D interlocking models created by our approach: 8-parts Bimba, 10-parts Mickey, 16-parts Rabbit, 10-parts Vase, 16-parts Pumpkin, and 20-parts Buddha (from left to right)
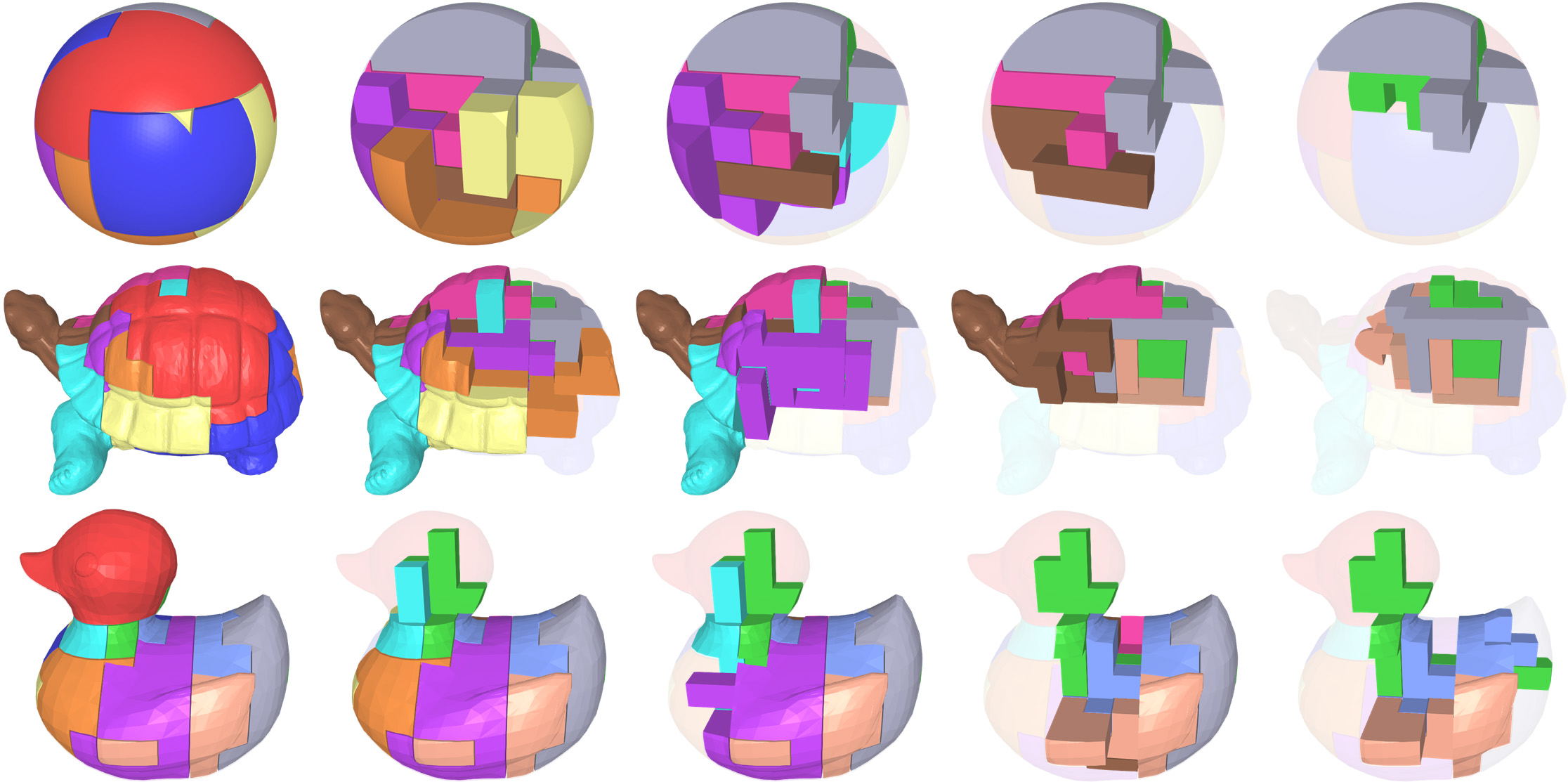
Figure 3: Assembly of a 10-parts Ball (top), a 12-parts Turtle ( middle), and a 12-parts Duck (bottom).
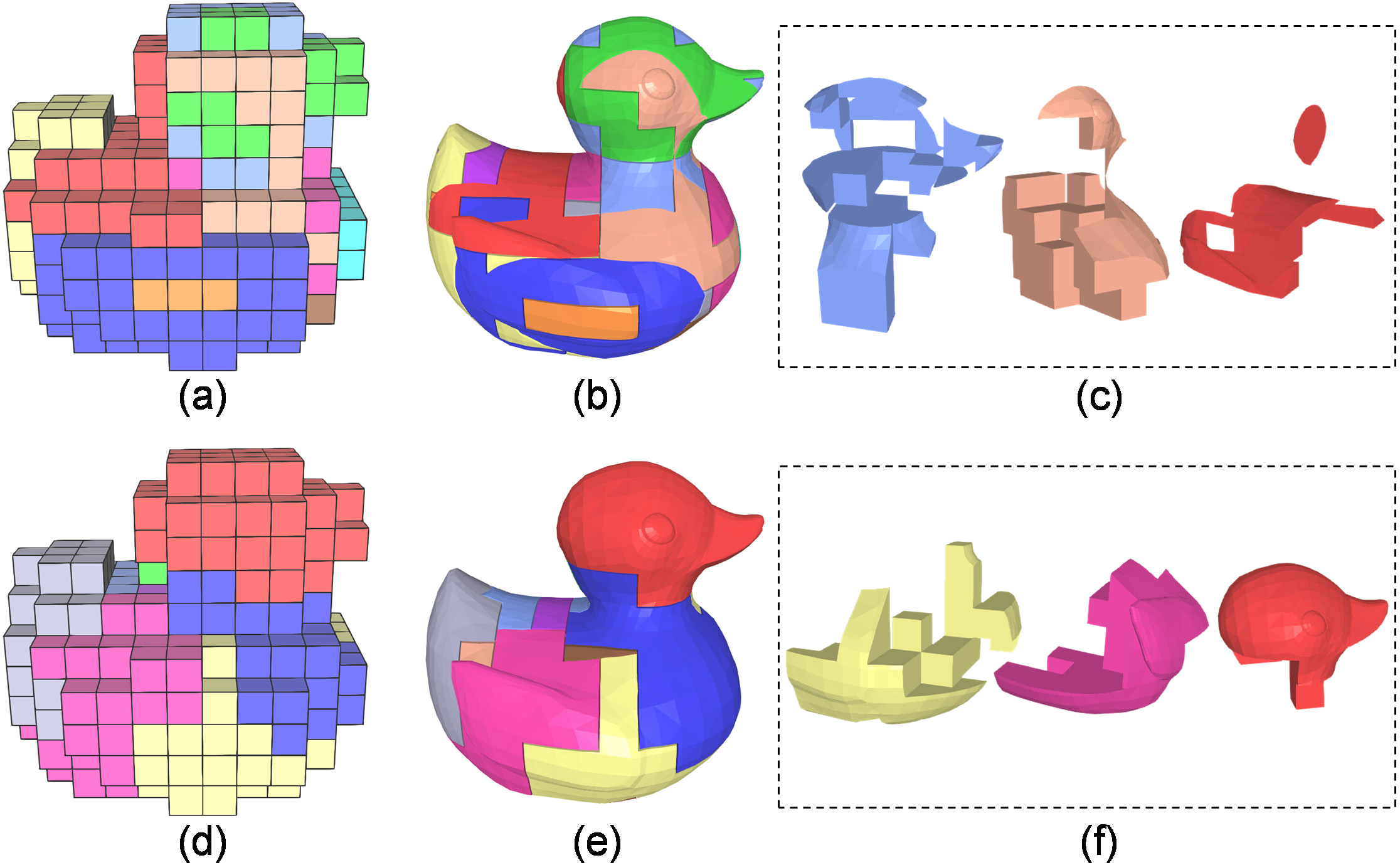
Figure 4: Duck (12 parts) created by [Song et al. 2012] (top) and our method (bottom). (a&d) Voxelized 3D parts assembly; (b&e) CSG-refined parts assembly; and (c&f) three example 3D parts.
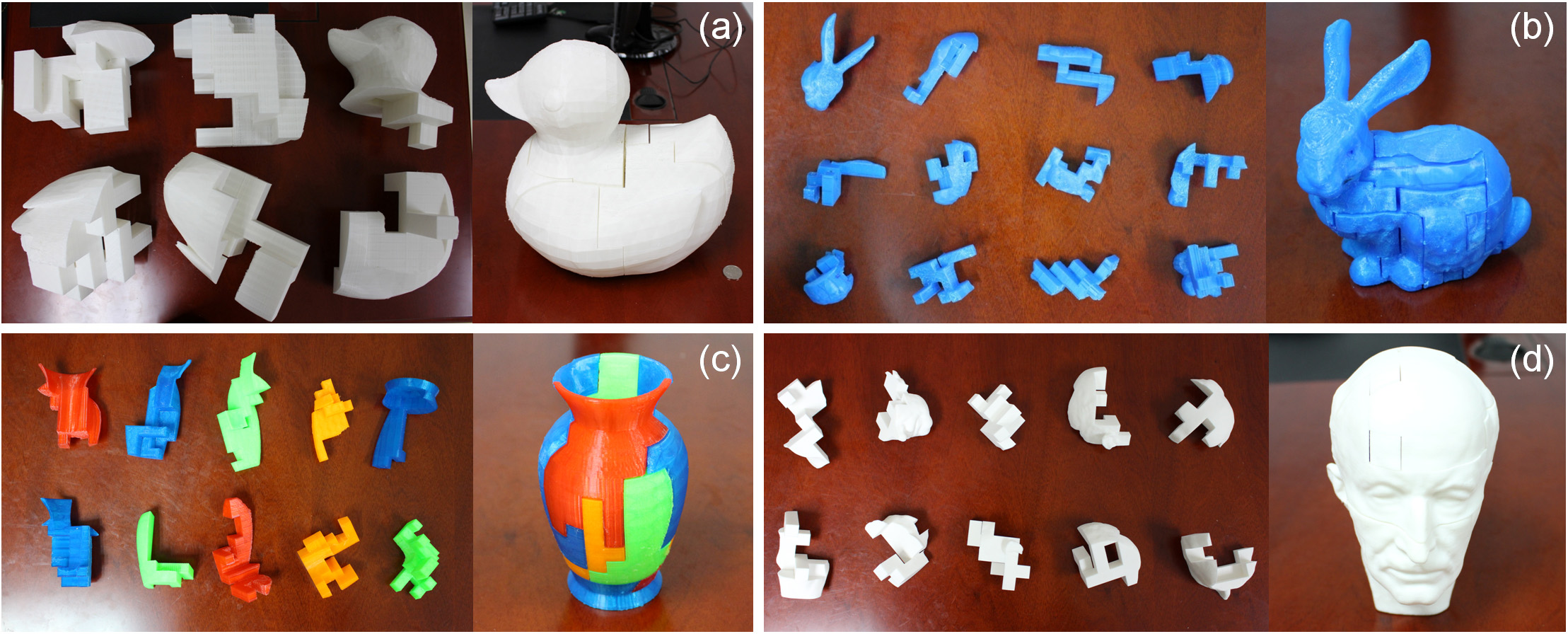
Figure 5: 3D-printed interlocking parts (left) and the corresponding assembled object (right). (a) 6-parts Duck by FDM; (b)12-parts Bunny by FDM; (c) 10-parts Vase by FDM; and (d) 10-parts Maxplanck by SLS.
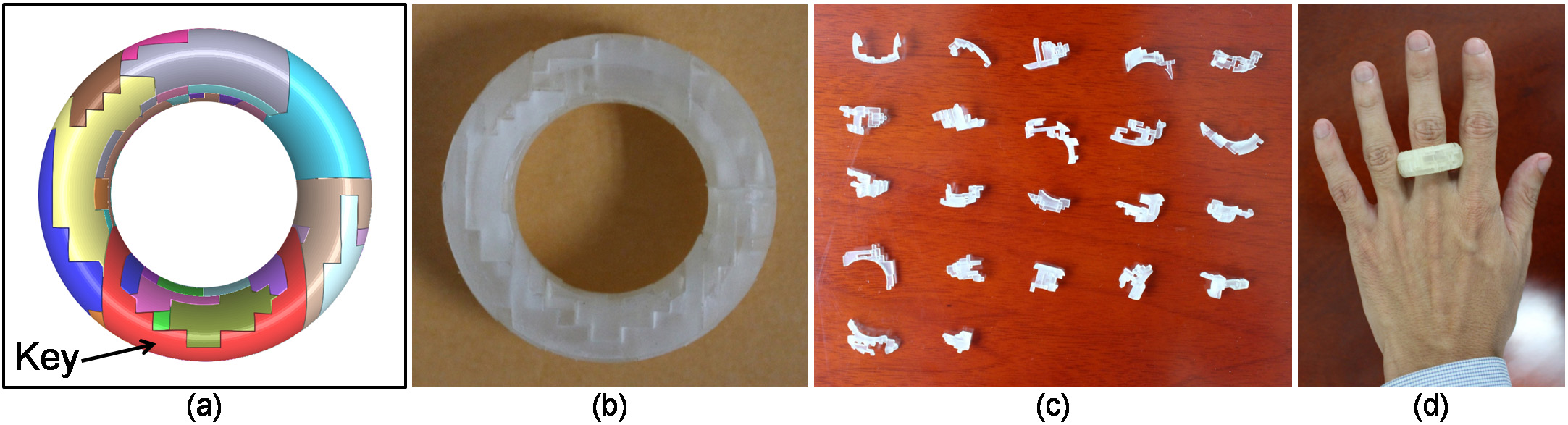
Figure 6: The 22-parts interlocking ring created by our method. (a) Virtual puzzle ring model; (b) the fabricated (assembled) ring model; (c) the twenty two 3D parts, individually printed by SLA; and (d) the ring being worn on a finger.
Acknowledgments:
The authors would like to thank Yael Friedman, a jewelry designer, for her various helpful comments on designing the 22-parts interlocking ring. The project is partially supported by the National Natural Science Foundation of China (61403357, 61222206), the Fundamental Research Funds for the Central Universities (WK0110000044), One Hundred Talent Project of the Chinese Academy of Sciences, and MOE AcRF Tier2 funding (MOE2011-T2-2-041 (ARC 5/12)), Singapore.
Bibtex:
@article {Song-2015-Interlock,
title = {Printing 3D Objects with Interlocking Parts},
author = {Peng Song and Zhongqi Fu and Ligang Liu and Chi-Wing Fu},
journal = {Computer Aided Geometric design (Proc. of GMP)},
volume = {35-36},
pages = {137-148},
year = {2015},
}